A 25 year relationship with industrial hemp
A pioneer and well respected champion of hempcrete, Klara Marosszeky, Founder & Managing Director of
Australian Hemp Masonry shares her 25 year relationship with industrial hemp.
By Kieren Anderson
Can you describe the journey of the Australian Hemp Masonry Company from its inception in 1999 to its current position in the hemp construction industry?
KM: The company was officially registered in 2014, but my involvement began in 1999 when I held a research licence with the Department of Health to conduct hemp varietal trials in New South Wales (NSW). At that time, DPI’s research suggested that hemp was not viable in NSW. I was one of the few licensed growers, holding licence number 3.
In 2000, after reviewing available research, I created trial mixes of hempcrete and sent them to my brother for his expert opinion. He had extensive experience in building materials research and would provide a cautious assessment. I grew 2 hectares of Futura 75 hemp in Wollombi, harvesting it with a small group using a brushcutter. We built a mini processor at the University of New South Wales (UNSW)
and began a self-funded research project at the Australian Centre for Construction. Progress was slow due to part-time teaching, work with Greening Australia, and a young family.
What were some of the initial challenges you faced when introducing hemp as a building material in Australia, and how did you overcome them?
KM: Initially, there was no precedent in Australia, apart from a Tasmanian project using imported materials. Limited English research on hemp building and minimal technical support presented challenges. The first significant hemp project in the UK, involving two townhouses in Suffolk, was completed in 2001. We faced a steep learning curve in understanding hemp construction and its adaptation to Australia’s diverse climates. This led to the development of a construction manual detailing best practices for hempcrete in Australia. We provided
one-on-one technical support for builders and owner-builders, addressing challenges such as extreme weather events like Cyclone Oswald in 2013.
Could you elaborate on the research and development process behind your building products? What were the key milestones and findings during this phase?
KM: Early on, we explored achieving load bearing hempcrete, misled by online claims about its high strength. We later realised that hemp’s true benefits lie in its carbon sequestration, thermal performance, vapour permeability, the improved indoor air quality it gave, rather than its load-bearing capacity. We also learned that while adding excessive binder could create a load-bearing material, it compromised other important properties of hempcrete.
How do you ensure the quality and durability of your hemp building products, especially considering the diverse climates they are used in across Australia and New Zealand?
KM: Ensuring quality and durability involves using well-tested products, reliable manufacturers, and understanding climate-specific installation challenges. Training installers, collaborating with building designers, and providing strong technical support are crucial. Educating builders and designers will be an ongoing task until hemp construction becomes mainstream.
We share insights from diverse projects in our training courses. With more published information and guidebooks, with recommended detailing, we can address various climate conditions in Australia, from cold and wet areas to hot and dry regions, as well as high humidity areas.
How have partnerships and collaborations with regional processors influenced the evolution of your products and the scalability of your operations?
KM: Emissions reduction was a core part of our vision, so regional partnerships and collaborations were essential. Introducing a novel building product like hemp required demonstrating its benefits plus its emissions reduction potential to stakeholders, including politicians. Building examples and partnerships across the country helped us gain acceptance and support.
Can you share some insights into the regulatory environment surrounding hemp construction materials in Australia? How has it evolved over the years?
KM: The regulatory environment has improved significantly. We now receive serious consideration from certifiers and building surveyors. Media coverage, such as on the ABC, has become more informed and positive. Most projects require development consent and certifier approval. We can provide a site-specific Performance Solution, documented product testing and international research to show how our materials meet National Construction Code standards. We also ensure designs are suitable for hemp construction, considering factors like roof overhangs and local weather. This year, we ‘re contributing to developing a Standards Handbook for Hemp Construction to hopefully further streamline approvals.
What are some notable residential and commercial projects where Australian Hemp Masonry products have been used? Could you highlight a few that demonstrate the versatility and performance of your materials?
KM: Notable projects include the Mildura Powerhouse Project, which features three buildings funded by federal, state, and regional governments.
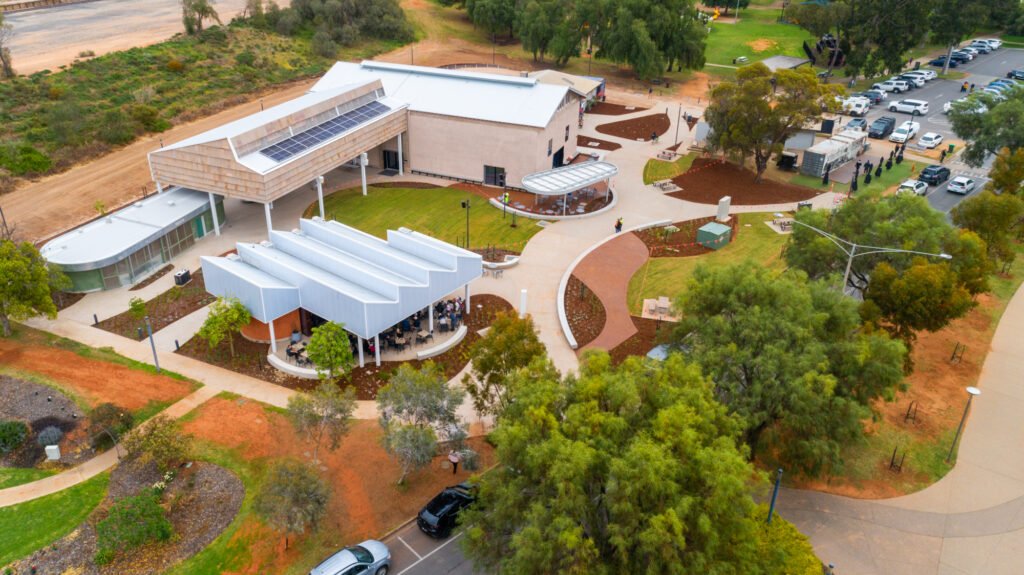
Innovation Centre at Byron Steiner School is Australia’s first hemp school building, praised for its carbon sequestration benefits and improved indoor climate. The award-winning hemp composting loo at Wilkins Green Public School in Sydney introduced hemp construction to city residents. The Caloundra hemp home, built by the community for a family with medical needs, highlighted hemp’s suitability for community projects.

In terms of sustainability, Shepherds Ground Ecovillage in the Hunter Valley showcases eight small-footprint hemp homes built with locally grown hemp and timber. Other notable projects include several award-winning homes in NSW and the upcoming refurbishment of the old Forestry building at UTAS’s Hobart Campus, featuring internal hemp walls.
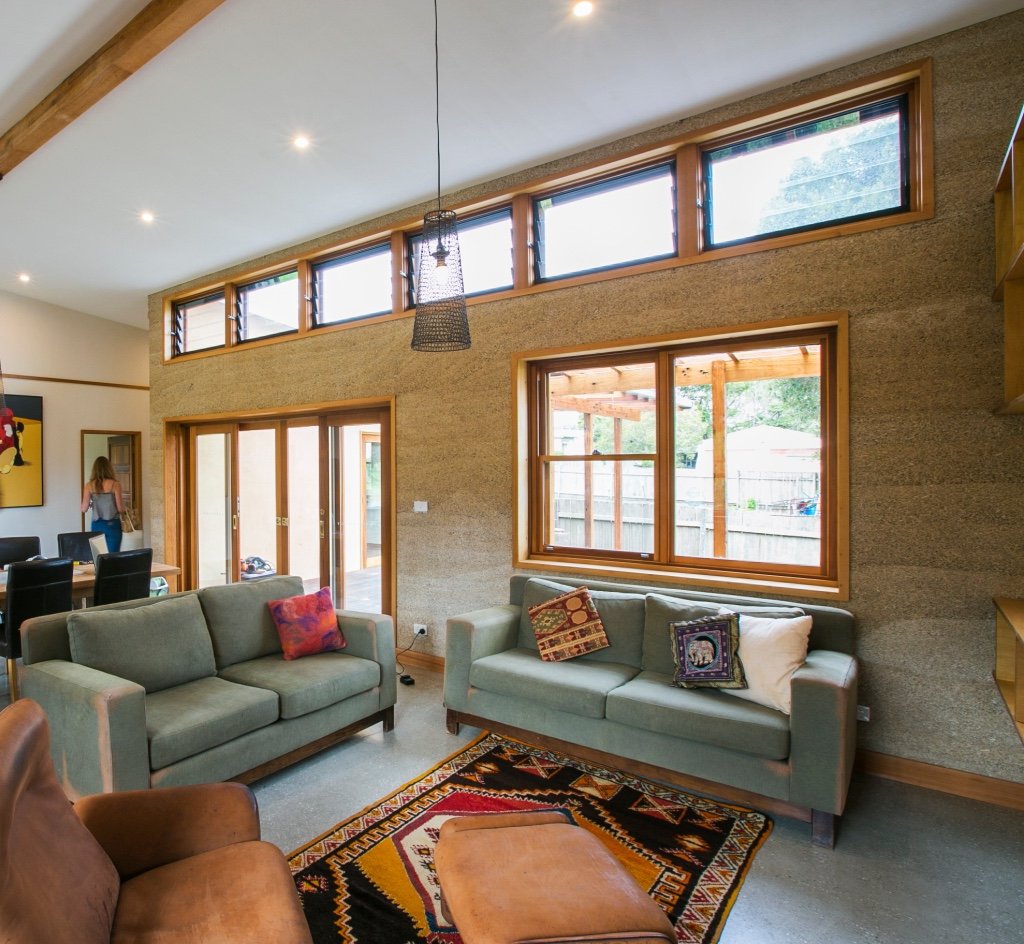

In what ways do you collaborate with architects, building designers, and builders to promote the adoption of hempcrete in construction projects?
KM: We often receive design enquiries from individuals who have attended our training courses and approach their designers with our details and compliance information. We engage in discussions with designers and builders, especially for first-time hemp projects. Collaborating with organisations like MECLA is helping us to attract the attention of design practices, developers, and government.
Looking forward, what are your goals and aspirations for the company in terms of innovation, expansion, and sustainability?
KM: We are continuously involved in R&D with universities, currently collecting data on thermals, acoustics, and indoor air quality at UTS. We aim to reduce costs while maintaining performance through prefab construction and material innovations. Our primary goal remains to establish hemp construction as a mainstream option. This is essential for addressing emissions reduction in the built environment and ensuring positive outcomes for future generations.
Visit Australian Hemp Masonry